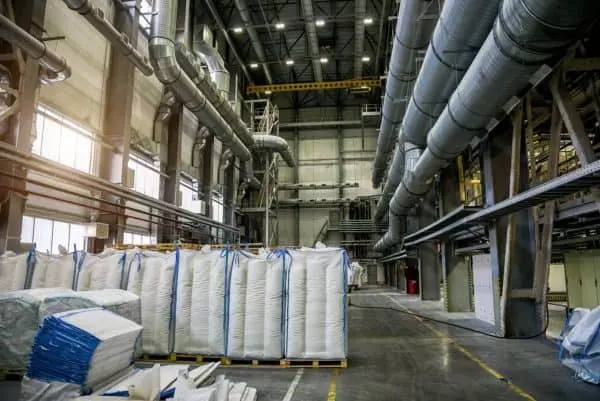
While asbestos use in the United States has declined quite steadily over the years, one industry in particular still relies on the mineral for its processes. Throughout the past few years, the chlor-alkali industry has used most or all of the asbestos imported into the U.S. In 2016, the EPA noted that 340 metric tons of chrysotile asbestos were imported and all of it was consumed by chlor-alkali plants.
Despite a decline in asbestos use in the U.S., the market is still growing in many other countries. The chlor-alkali industry in particular still uses asbestos on a global scale, with many plants in China also using toxic mercury processes. Though more and more plants, especially throughout Europe, have slowly adopted safer manufacturing methods, many still rely on these older asbestos or mercury involved methods that have been used for well over 100 years.
In addition to leaving a bigger carbon footprint and harming the environment, these older methods also put workers at risk for mesothelioma and other serious health problems.
What is the Chlor-Alkali Industry?
In essence, this industry is vital to the larger chemical industry, as well as various other aspects of our day-to-day lives. The chlor-alkali industry produces three essential products: chlorine, sodium hydroxide (also called caustic soda) and hydrogen.
Chlorine is the most important product manufactured, as it’s used in many chemical processes and industrial settings. For example, chlorine is used in countless products ranging from medical devices, 93% of American pharmaceuticals, insulation, and of course, helping to disinfect swimming pools. In most of these instances, researchers have found there’s no viable substitute for chlorine. In addition to providing better health and safety, chlorine is an important element for resource conservation and harnessing solar energy.
In the manufacturing of chlorine, the co-products of caustic soda and hydrogen are also vital for many other industries. Caustic soda, an alkali, is used often in the food industry, textile production and creating soaps and other cleaning agents. Hydrogen has many uses as well, most notably for the creation of hydrogen peroxide and ammonia.
Overall, the chlorine industry is a large producer around the world because these products are essential for so many aspects of our daily lives. Globally, 65 million tons of chlorine were produced in 2016, with 14 million produced in the U.S. and 10 million produced in Europe. In the United States alone, the chlor-alkali industry generates at least $8 billion each year in sales and employs approximately 20,000 workers directly, as well as creates thousands of other jobs in related industries.
Though chlorine manufacturing is vital for many applications and is largely considered to be a positive economic factor, some of the procedures in place for producing these materials are putting the workers at risk of asbestos exposure.
Asbestos Use in Chlorine Manufacturing
Manufacturing chlorine has been in practice for well over a century, though many plants still use more toxic and unsafe methods to produce it. In general, the industry relies on three basic manufacturing processes:
- The mercury cell process
- The diaphragm cell process
- The membrane cell process
All of these processes rely on the same basic chemistry. Chlorine and its co-products are created by electrolysing a salt solution with a direct electric current that ultimately converts chloride ions into chlorine. While the mercury cell process is decreasing globally and much of Europe has adopted the safer option of the membrane cell process, several plants in America still use diaphragms made from asbestos.
The diaphragm cell process works with a combination of water and sodium chloride to create a brine solution, which is processed and filtered to remove impurities. Heat is applied to the solution and more salt is added until the purified brine solution is prepared for the electric current, which is where the asbestos materials come into play.
An asbestos diaphragm is usually used to separate the cathode and anode, which will create the current. Though the United States Geological Survey noted in a recent asbestos study that more plants are looking for alternatives for the asbestos diaphragms, at least 15 plants in the United States still use these products today. According to the EPA, a typical plant will use anywhere from 5 – 25 tons of asbestos each year in production of these diaphragms.
The industry relied on making asbestos diaphragms because of the mineral’s durability and chemical resistance. These properties help the diaphragm prevent the caustic soda also being produced in the process from reacting with the chlorine.
The mercury process is just as dangerous, as workers apply liquid mercury for the cathode. Mercury exposure can cause a variety of health problems, some of which can be fatal. This manufacturing can also release mercury into the air, which can eventually accumulate in ecosystems and affect wildlife and the general population.
The membrane cell process is the newest method to produce chlorine and its products, and is regarded as the safest for both workers and the environment. This process relies on a membrane made of polymers that only allows positive ions to flow through, which means the remaining sodium chloride cannot contaminate the chlorine being produced. Polymers have no toxins that pose a risk for workers, and this method uses the least amount of energy and steam.
A Need for Change
While many in this industry have already made the production change to the safer membrane process or even alternatives for the asbestos diaphragm itself, there are still many plants holding back. They’re resisting change likely because of the time and investment needed to convert these plants to safer methods.
Experts note it can take anywhere from 1.5 to 2.5 years to convert a plant, depending on the facility. The estimated investment is about 40 – 50% of the cost of opening an entirely new plant, which experts say can be anywhere from $500 – $700 per metric ton of chlorine produced.
As long as the industry resists change, workers in these dangerous settings need to understand their rights and take action to protect themselves. Hopefully, the industry will change on its own sooner rather than later, and not simply wait for a ban on asbestos to force better safety at work.